Salt Spray testing
Salt spray corrosion is the most frequent and harmful type of atmospheric corrosion because it occurs naturally. The chloride ions in salt spray will pierce the protective layer and oxide layer on the surface of metal materials, engage in an electrochemical reaction with the internal metal, destroy the surface and properties of the metal materials, and further contaminate and harm the finished goods through the pores and cracks in the metal surface.
The corrosion resistance of items or metal components is tested using a salt spray test, a type of environmental test that simulates the environmental conditions of salt spray. You can decide whether a certain fastener is durable enough to satisfy your demands by looking at the corrosion resistance test results of a material or coating.
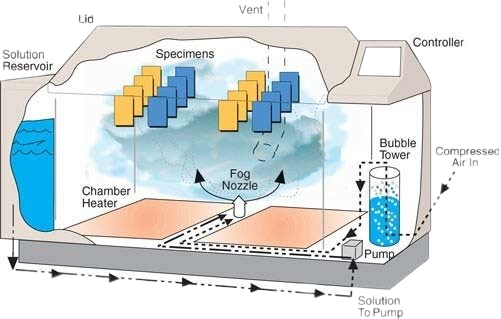
We offer a variety of test techniques, including but not restricted to:
Neutral Salt Spray Test (NSS)
– Applicable scope: metal coating anodizing film, organic coating on metal substrate
The earliest and most popular method for testing accelerated corrosion is the neutral salt spray test. Through a spray apparatus, salt water with a pH of 6.5–7.2 and a concentration of 5% NaCl is sprayed into a designated test chamber. The salt spray settles on the test sample, and after a predetermined amount of time, the surface corrosion state is assessed. The test chamber is (352)°C, has a humidity level of above 95%, reduces fog by 12mL/(hcm2), and has a nozzle pressure of 78.5137.3kPa (0.81.4kgf/cm2).
Acetate Salt Spray Test (ASS)
Applicable scope: Aluminium anodic oxide film, copper-nickel-chrome or copper-chrome ornamental coating
Based on the Neutral Salt Spray Test, the Acetate Salt Spray Test was created. It is necessary to add some glacial acetic acid to the 5% NaCl solution in order to alter the final salt spray from neutral to acidic and lower the pH value of the solution to around 3. Its rate of corrosion is almost three times that of the NSS test.
Copper Accelerated Acetic Acid Salt Spray Test (CASS)
Applicable scope: Aluminium anodic oxide film with decorative copper-nickel-chrome or nickel-chrome coating
An accelerated test procedure specifically created to assess copper-nickel-chromium or multilayer nickel-chromium is the copper accelerated acetic acid salt spray test. In order to simulate a harder working environment, CuCl2 (0.260.02) g/L is added to the spray liquid based on the results of the acetate salt spray test. This causes the influence of copper ions to accelerate battery deterioration. It corrodes at a pace that is around eight times faster than the NSS test.
Alternating Salt Spray Test
Applicable scope: Metal substrate with an organic coating and an anodizing layer.
Alternating Salt Spray Test is a complete salt spray test that combines a continual damp-heat test with a neutral salt spray test. It is mostly utilized for cavity-type machine items. As a result of tidal environment penetration, salt spray corrosion affects both the product’s exterior and interior. It alternatively transforms the products in a hot, humid environment and a salt fog before checking to see if the mechanical and electrical qualities of the entire machine have altered.
Standards we test to
ASTM B117 | Standard Practice for Operating Salt Spray (Fog) Apparatus |
ISO9227 | Corrosion Tests in Artificial Atmospheres |
JIS Z 2371 | Methods of Salt Spray Testing |
ASTM G85 Annex A1 | Acetic Acid Salt Spray Test (non-cyclic) |
ASTM G85 Annex A2 | Acidified Salt Fog Test (cyclic) |
ASTM G85 Annex A3 | Seawater Acidified Test (cyclic) |
ASTM G85 Annex A4 | SO2 Salt Spray Test (cyclic) |
ASTM G85 Annex A5 | Dilute Electrolyte Salt Fog/Dry Test (cyclic) |